ruggedised AI vision hardware
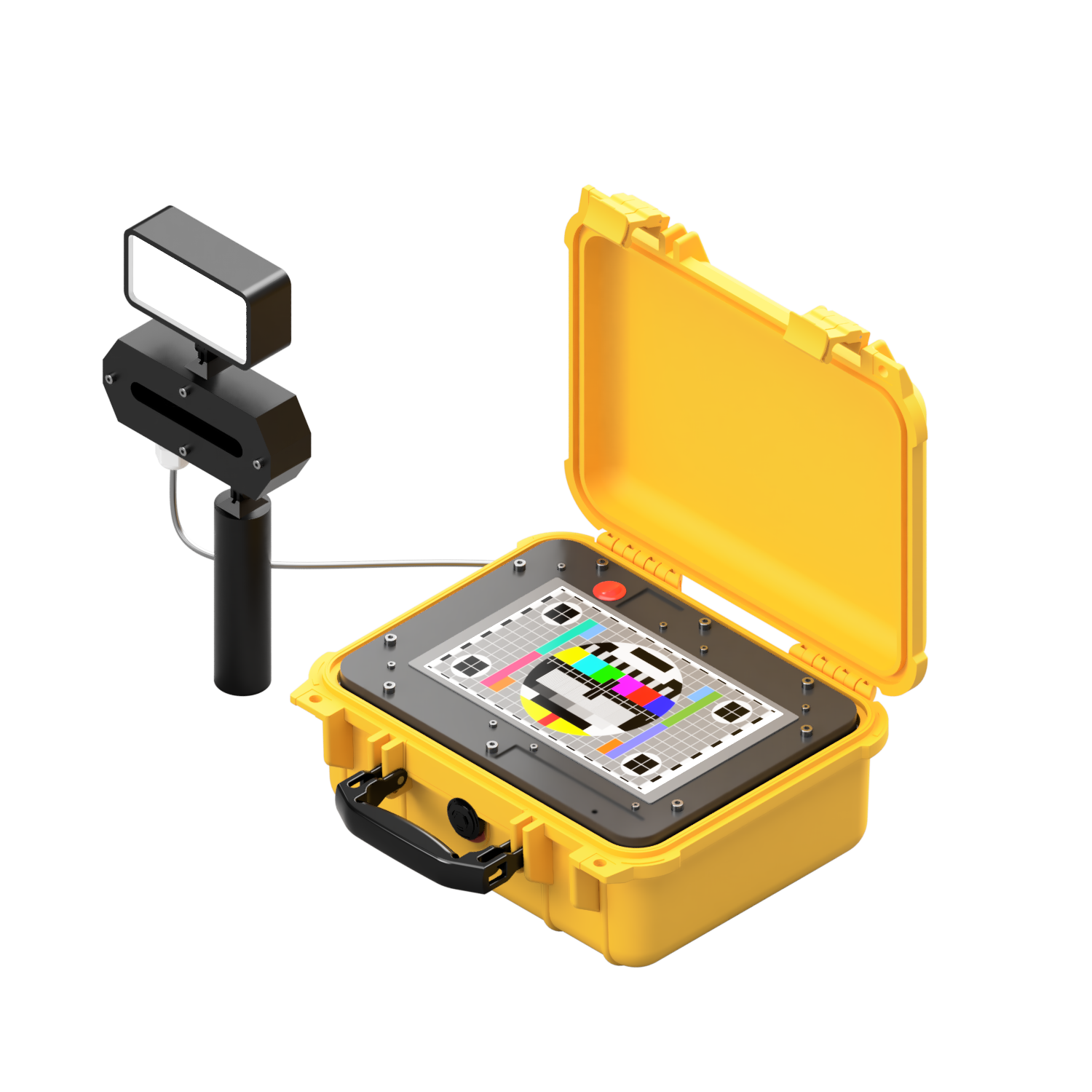
client
RAIL
role
DATA ACQUISITION, HARSH ENVIRONMENTS
year
2020
This project involved the design and development of a ruggedised machine vision processing system, built to handle AI-driven image analysis in harsh environments. The system was designed with high durability in mind, featuring an IP-rated plastic hard case, industrial connectors, and bespoke camera housing. It included capabilities for remote access and Over-the-Air (OTA) updates, ensuring efficient operation and maintenance in the field. The following stages detail the project:
1. Requirements Analysis & Design
The project began with defining the requirements for a machine vision system that could operate in challenging industrial environments. The system needed to process AI workloads for real-time image analysis, and its design had to withstand harsh conditions such as dust, moisture, and temperature extremes. Industrial-grade connectors and a robust housing were essential for both durability and reliable long-term operation.
2. Hardware Development
A ruggedised processing unit was developed, capable of handling the demanding computational requirements of AI-driven vision processing. The unit was encased in a custom plastic hard case, specifically designed to meet IP rating standards, providing protection against water, dust, and mechanical shocks. Industrial connectors were used for power and data interfaces, ensuring the system could be deployed in a range of industrial environments without risk of failure.
3. Bespoke Camera Housing
A custom-designed camera housing was developed to accommodate the vision sensors, protecting them from environmental damage while allowing precise image capture. The housing was engineered to ensure optimal placement of the camera lenses, with attention to vibration damping and weather resistance, ensuring the camera could capture high-quality images under varying conditions.
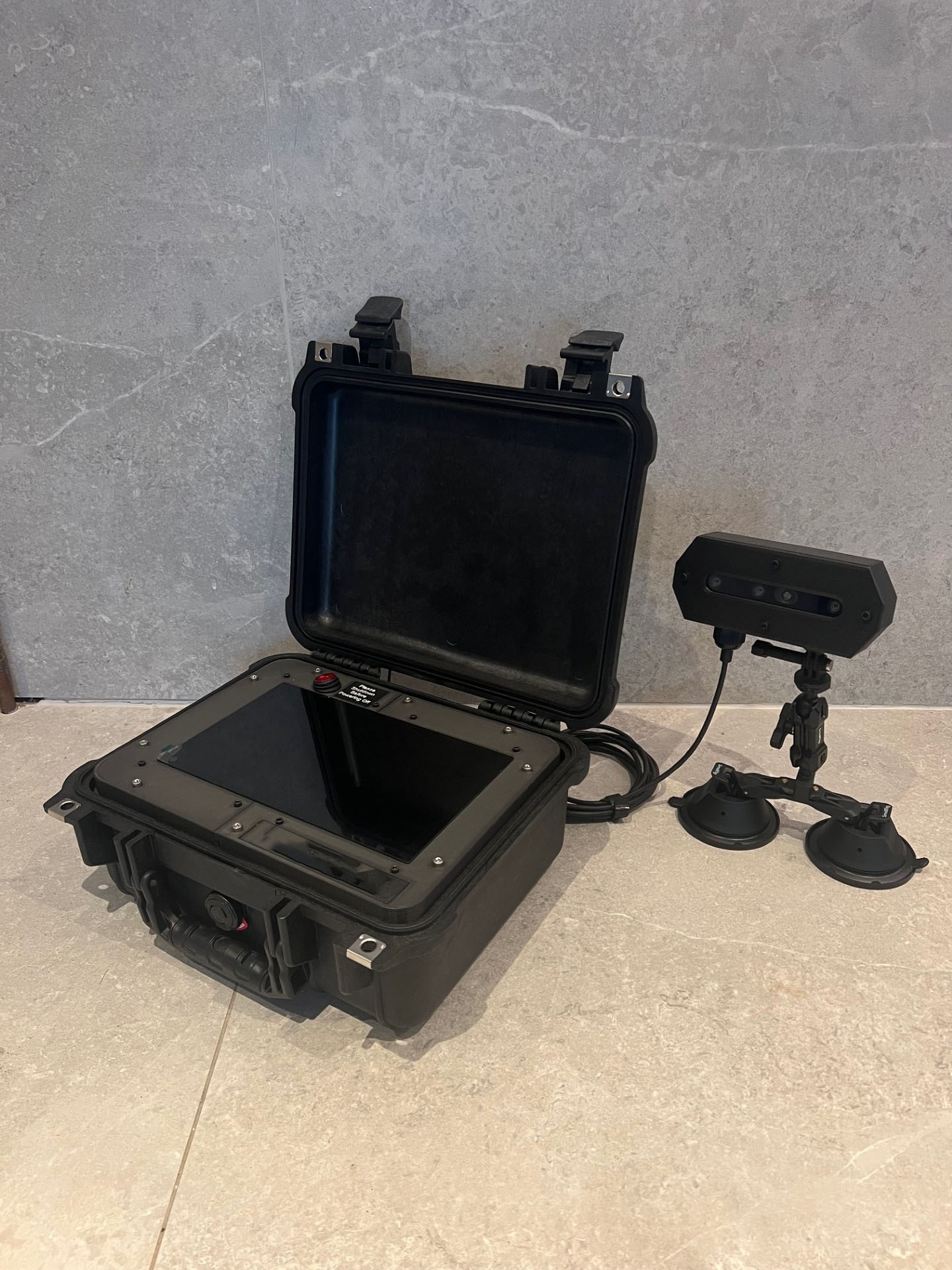
4. Remote Access & OTA Capabilities
The system was designed with remote access capabilities, allowing operators to monitor and manage the machine vision system from any location. This included real-time access to the AI processing results, as well as control over system parameters and diagnostics. Additionally, Over-the-Air (OTA) update functionality was integrated, allowing software and firmware updates to be pushed remotely, ensuring the system remained up-to-date without the need for on-site intervention.
5. Prototyping & Testing
Prototypes of the ruggedised system were developed and subjected to rigorous testing in industrial conditions. The system was tested for its resilience against dust, water ingress, temperature fluctuations, and mechanical impacts, ensuring the IP rating was fully validated. The camera housing was also tested to confirm the protection it provided while maintaining high image quality. Performance testing confirmed the system could reliably process AI workloads and deliver accurate results in real-time.
6. Deployment & Maintenance
Once testing was complete, the ruggedised system was deployed in the field. The IP-rated enclosure and industrial connectors ensured reliable performance in harsh environments, while the bespoke camera housing allowed for clear, consistent image capture. Remote access allowed operators to monitor and control the system without needing to visit the installation site, and OTA updates ensured the system could be maintained and upgraded seamlessly over time.
7. Results & Scalability
The machine vision processing system successfully operated in the field, providing accurate AI-driven image analysis under tough conditions. The robust design ensured minimal downtime, while the remote access and OTA capabilities reduced the need for physical maintenance. The system demonstrated scalability, with potential for deployment across a variety of industrial applications where ruggedness and real-time AI processing are required.
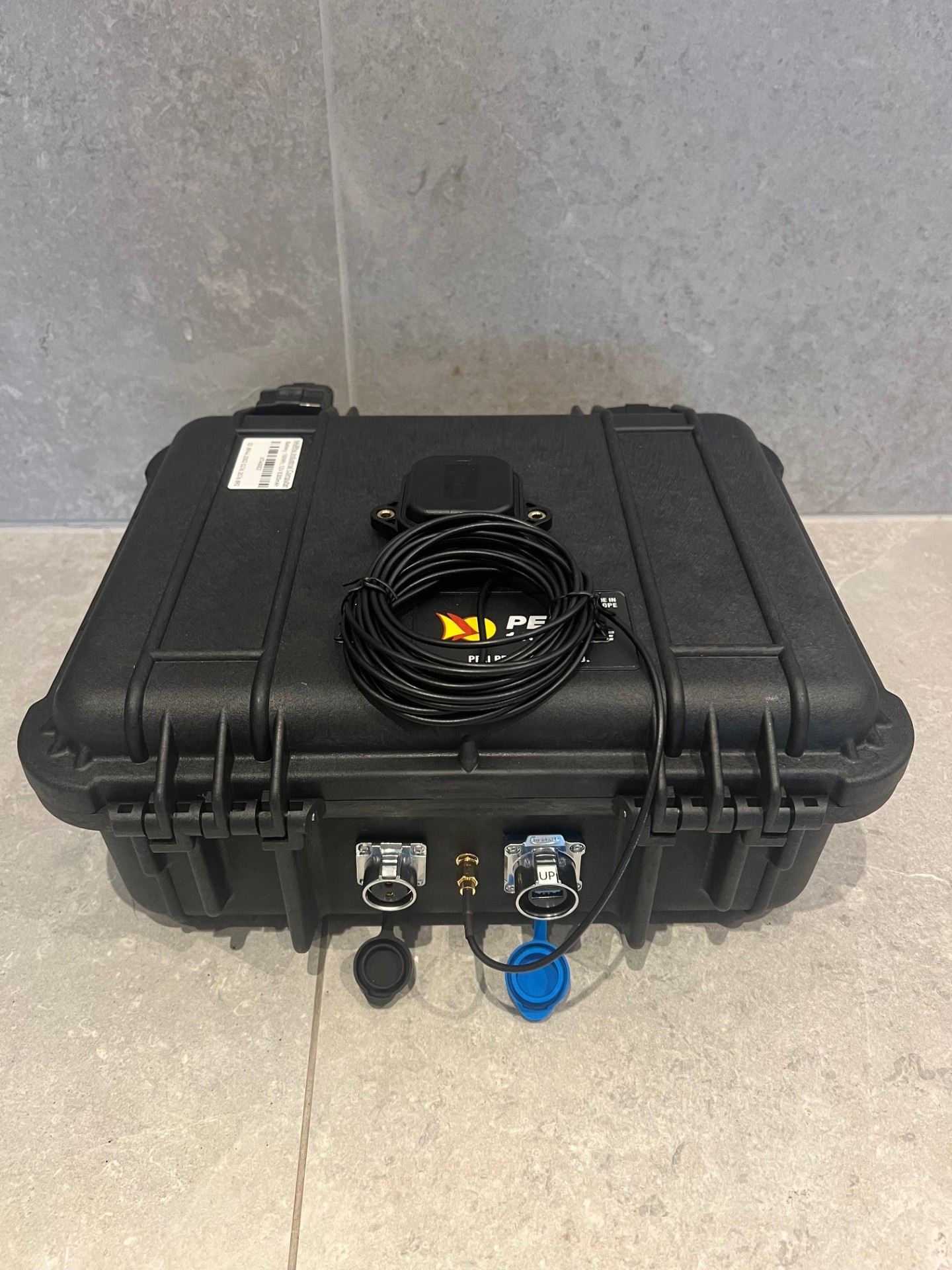